stretch film extrusion screen changers
Introduction to Casting Film Screen Changer
The production of biaxially stretched casting film and paper coated film has extremely high requirements for the sealing of the screen changer, and the production temperature is also high. Therefore, ordinary screen changers will basically encounter leakage or seepage problems. The Bart casting film and coated film dedicated screen changer adopts a rigid sealing structure design, and at a high temperature of 340 ℃, the screen changer is produced normally without leakage or seepage.
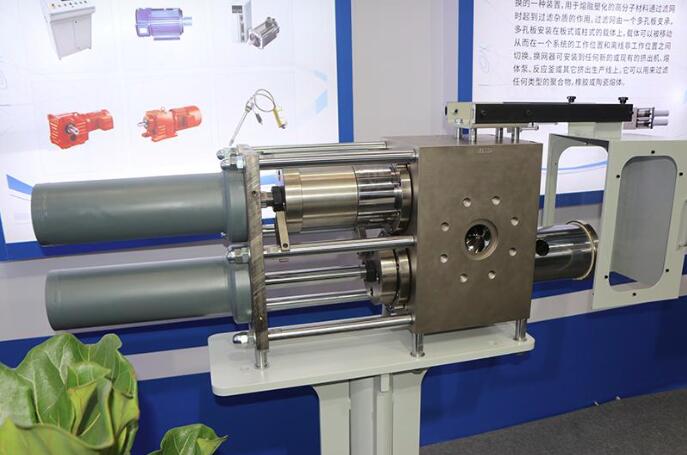
Working Principle of stretch film extrusion screen changers
The stretch film extrusion screen changers adopts a dual column and dual channel design, with internal heating, fast heating, and uniform temperature. During normal production, both filter screens work simultaneously. When replacing the filter screen, one filter screen works and the other filter screen is replaced. A material introduction and exhaust device is designed, which is controlled automatically or manually to achieve non-stop screen change, no material leakage, uninterrupted material flow, small material pressure fluctuation, little impact on production, and good continuity. Suitable for production under various working conditions with continuity requirements.
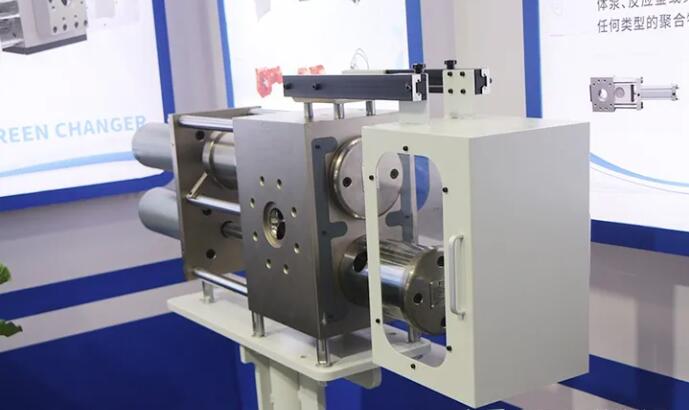
Characteristics of Bidirectional Stretch Casting Film Screen Changer
1. Dual channels, dual workstations, dual networks working simultaneously;
2. Alternate replacement of dual networks to ensure the normal production process;
3. The curved filter design effectively increases the filtering area;
4. Rigid sealing structure, no leakage;
5. Progressive feeding and exhaust structure, with small pressure fluctuations during the mesh changing process, ensuring continuous and stable product production;
6. Optimize the design of the internal flow channel, without dead corners or stagnant flow;
7. It can achieve automatic alarm and control, ensuring the safe and stable operation of the system.
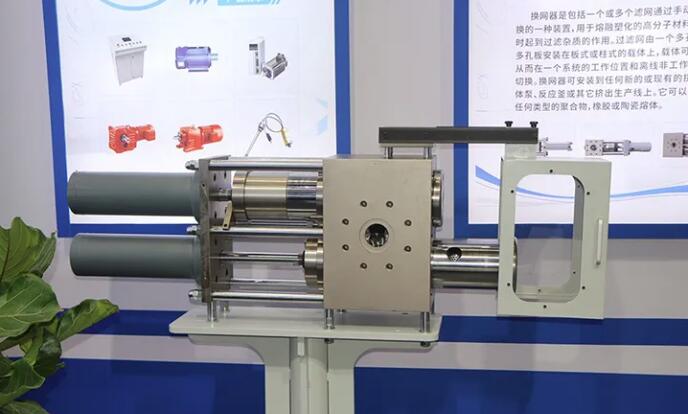
Advantages of Stretch Casting Film Hydraulic Screen Change
The production of cast film generally adopts a dual column and dual station hydraulic non-stop screen changer. The advantage of using a dual column and dual station is to avoid long-term insulation and heating of the backup filtration station outside the screen changer body, aging of the raw materials in the screen plate, and a certain temperature difference between the temperature and production temperature, which will have a certain impact on production after screen replacement. For the production of PE/PP film, if it is to meet the requirements of continuous production without stopping, the dual column and dual station non-stop screen changer can also meet its needs, with a pressure of 35MPA, no impact on continuous production, and no material leakage. It is a very good choice.
Email: info@battemachinery.com
Whatsapp: +86 158 38331071