Working principle and application field of dual channel plate non-stop screen changer
The operation of the dual channel plate non-stop screen changer is based on two parallel sliding plates inserted into the main body of the screen changer, each of which is designed with a circular filtering station. These two circular filter screens work simultaneously, and the high-temperature melt is divided into two channels through the inlet of the screen changer. After passing through the filter screens on both sides, it is collected in the screen changer and finally flows through the outlet into the mold. When impurities accumulate on the filter screen to a certain extent, the pressure alarm will sound an alarm, and a screen replacement operation is required at this time.
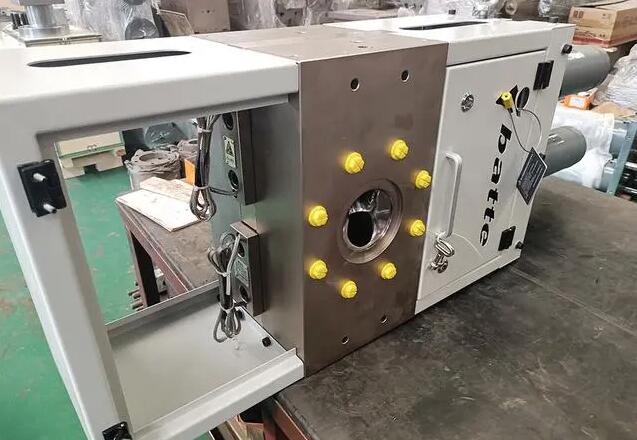
During the screen changing process, operate the handle button on the hydraulic station to start the hydraulic station. Press the push button on the corresponding column on the operation handle to push one of the sliding plates for displacement, causing the filtering station to move out of the main body of the screen changing device. At the same time, the filtering station on another skateboard is still performing filtering work, ensuring the continuity of the production process. After the station is moved out, close the hydraulic station, clean the filter station of the removed main body, and replace it with a new filter screen. Then start the hydraulic station again, press the corresponding sliding plate pull button on the operating handle of the hydraulic station, and pull the sliding plate back into the main body to continue working.
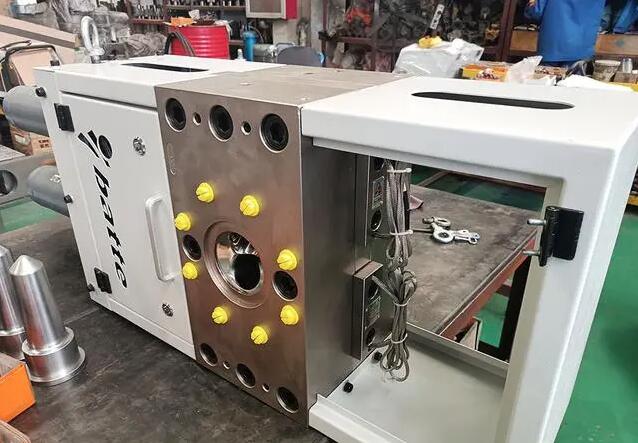
The dual channel plate type non-stop screen changer is widely used in various industrial fields, especially in the production of chemical fibers, blown films, flat films, and cast films, as well as in the manufacturing of pipes, plates, wires, fibers, cutting lines, recycling, and other aspects, with significant advantages. Due to its dual channel and dual filter structure, as well as the design of feeding and exhaust, the mesh changing process can be carried out without interrupting the material flow, achieving non-stop mesh changing, greatly improving production efficiency and product quality. In addition, the dual plate and dual station non-stop screen changer is also suitable for all polymer extrusion production requirements, and can withstand melt pressure of 25-30Mpa without affecting its performance.
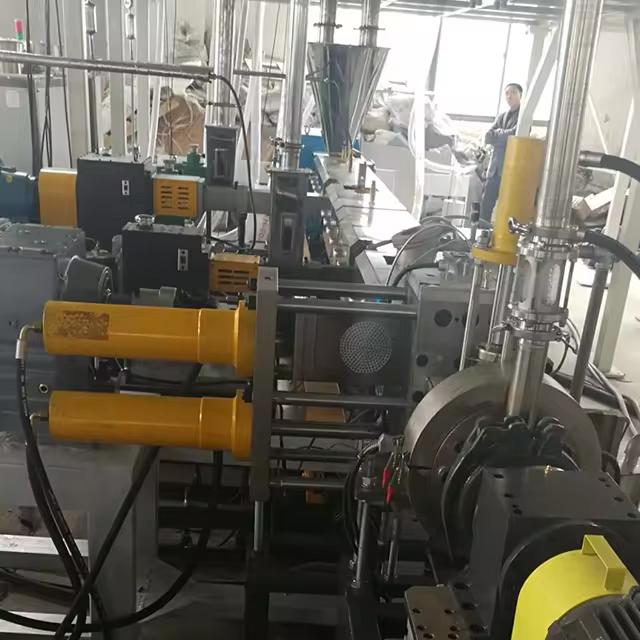
Overall, the dual channel plate type non-stop screen changer plays an important role in industrial production due to its high efficiency, stability, and reliability.
Email: info@battemachinery.com
WhatsApp: +86 158 38331071