What is the role of the epoxy resin twin-screw extruder screen changer in the production line?
The screen changer of epoxy resin twin-screw extruder is a key equipment on the production line, and its importance is self-evident. It plays a crucial role in the entire production process, not only related to product quality, but also directly affecting production efficiency. Next, we will discuss in detail the role of the screen changer in the epoxy resin twin-screw extruder on the production line.
Firstly, one of the main functions of the screen changer in the epoxy resin twin-screw extruder is to filter out impurities in the raw materials. In the production process, it is inevitable that some impurities, such as foreign objects and fine particles that have not been plasticized, will be mixed into the raw materials. If these impurities are not filtered, they will directly affect the quality and performance of the product. The screen changer can effectively intercept and remove these impurities through its internal filter plate, ensuring that the raw materials entering the extruder are pure, providing strong guarantee for producing high-quality products.
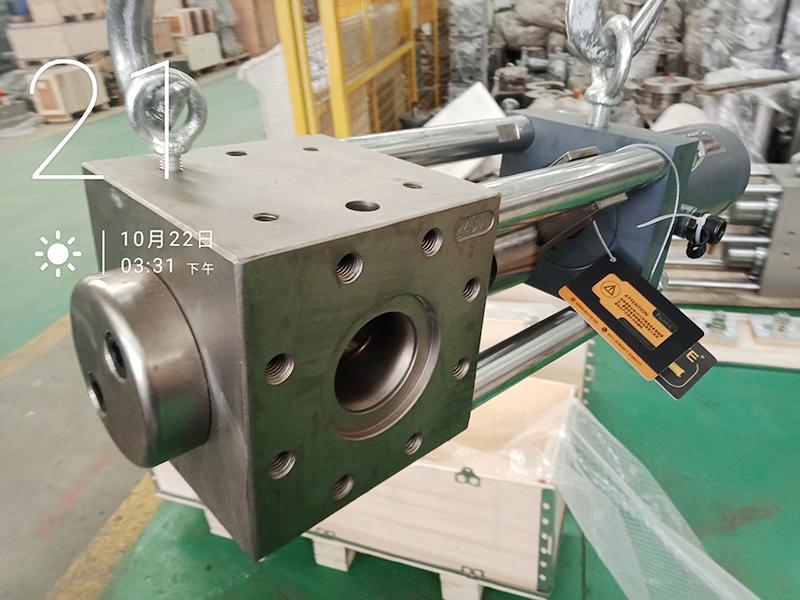
Secondly, the screen changer can improve the plasticization and homogenization effects of raw materials. During the extrusion process, the raw materials need to go through two key steps: plasticization and homogenization to ensure that the product has a uniform texture and good smoothness. The addition of a screen changer can increase the back pressure of the machine head, enabling better plasticization and homogenization of the raw materials during the extrusion process. This not only improves the texture and appearance quality of the product, but also helps to enhance the pressure resistance value of the product, making it safer and more reliable during use.
In addition, the screen changer can also change the rheological behavior of materials. During the extrusion process, the material needs to undergo a transition from rotary flow to linear flow. Traditional extruders may experience unstable and uneven material flow without a screen changer, which can lead to defects such as "tangled lines" in the product. After adding the mesh changer, the flow behavior of the material in the channel is optimized, making the cross-sectional flow rate of the entire melt as consistent as possible, avoiding the occurrence of "polymer orientation" and laminar flow phenomena. This not only improves the longitudinal strength of the product, but also reduces the transverse strength, making the product more in line with usage requirements.
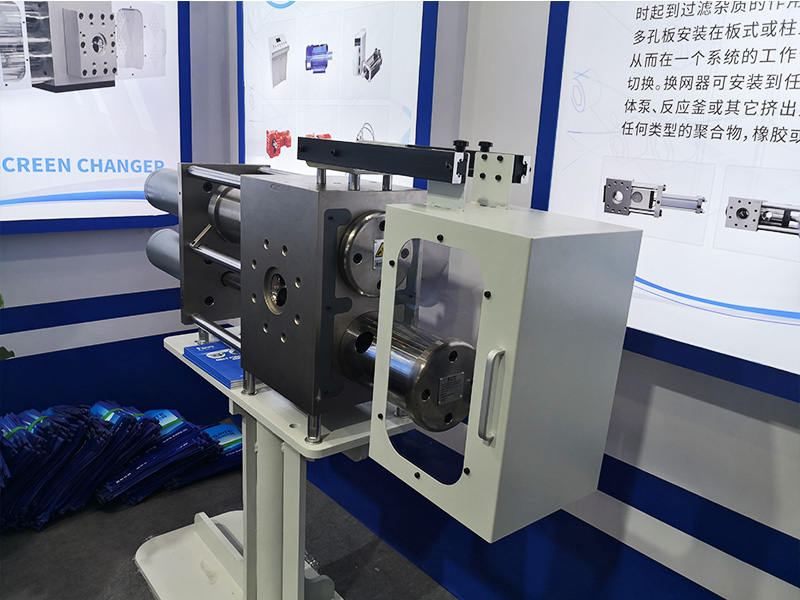
At the same time, the screen changer also helps to eliminate water vapor and volatile substances in the raw materials. During the extrusion process, the raw materials may contain a certain amount of water vapor and volatile substances, which, if not treated, can have adverse effects on the quality and stability of the product. The screen changer can effectively remove these water vapor and volatile substances through its internal structural design, thereby ensuring the purity and stability of the product.
In addition, the screen changer can also reduce the wear of impurities on the mold. During the extrusion process, the presence of impurities not only affects product quality, but also causes wear on the mold. Under long-term use, the wear of the mold will gradually intensify, leading to a decrease in production efficiency and unstable product quality. The use of a screen changer can effectively filter out these impurities, reduce their wear on the mold, thereby extending the service life of the mold and reducing production costs.
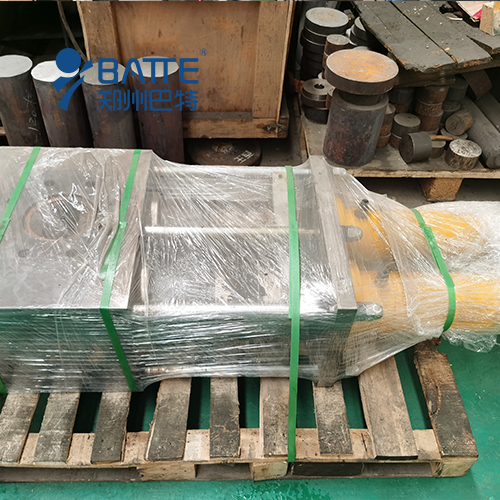
Finally, it is worth mentioning that modern twin-screw extruders have achieved online screen changing function. This means that during the production process, there is no need to shut down the machine to perform screen changing operations, greatly improving production efficiency. At the same time, online mesh changing technology can also ensure uninterrupted material flow, small material pressure fluctuations, minimal impact on production, and good continuity in the production requirements during the mesh changing process.
In summary, the role of the epoxy resin twin-screw extruder screen changer in the production line cannot be ignored. It can not only filter impurities in raw materials, improve the plasticization and homogenization effect of raw materials, change the rheological behavior of materials, eliminate water vapor and volatile substances in raw materials, but also reduce the wear of impurities on molds and improve production efficiency. Therefore, it is necessary to choose a suitable screen changer on the production line of epoxy resin twin-screw extruder.
Email: info@battemachinery.com
WhatsApp: +86 158 38331071