How to choose the type of plastic sheet extrusion screen changer?
The screen changers for plastic sheet extrusion can be classified into various types based on their structural and operational characteristics. Below are some primary types, their characteristics, and the factors to consider when selecting a screen changer:
I. Main Types of Screen Changers for Plastic Sheet Extrusion
1.Discontinuous Screen Changers
Characteristics: The screen changing process requires manual operation, leading to slower changeovers, suitable for small-scale pilot lines or intermittent production processes. They feature a simple structure but cause relatively large pressure fluctuations during screen change, which may necessitate brief downtime.
Application Areas: Primarily used in processing pure-color materials, producing small batches of color masterbatches, and compounding production.
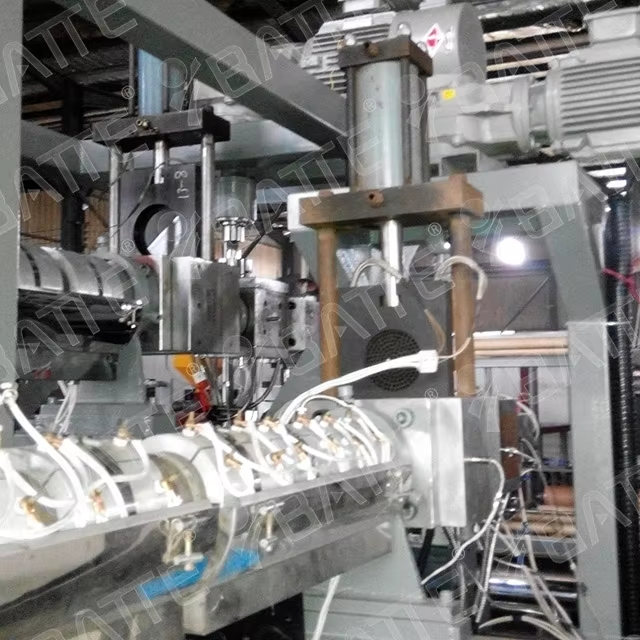
2.Continuous Screen Changers
Hydraulic Screen Changers: Including single-plate dual-station, single-plate four-station, double-plate dual-station, single-column dual-station, double-column dual-station, double-column four-station, and double-column backflush hydraulic screen changers. Most of these allow for continuous production during screen change, ensuring stable material flow and minimal pressure fluctuations, minimizing the impact on product quality.
Belt-Type Automatic Screen Changers: Utilize a continuous belt-type filtration method, enabling automatic screen changes without manual intervention. Suitable for scenarios requiring short intervals between screen changes and high production continuity.
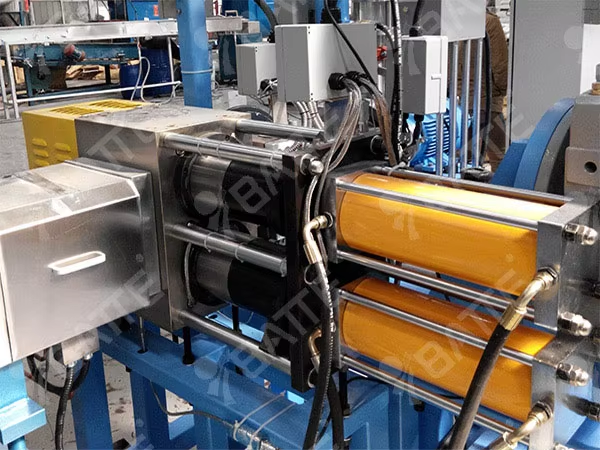
3.Manual Screen Changers
Characteristics: Easy to operate but require machine shutdown or reduced extrusion speed during screen change, suitable for applications with less stringent continuity requirements.
II. Factors to Consider When Selecting a Screen Changer
Production Demand: Adjust based on the customer's production volume, material composition (impurity content), and viscosity parameters, combined with the theoretical output of the screen changer, to meet production requirements.
Process Requirements: The impact of the screen-changing process on the production process is a crucial factor. Some screen changers may cause pressure fluctuations during screen change, affecting product quality. Therefore, it's essential to choose a screen changer that meets the process requirements.
User Demands: Users' requirements for screen changers vary based on their usage scenarios. Some prioritize stringent process requirements, short screen-changing intervals, reduced manual operations, while others focus more on cost. Balancing these specific demands is necessary when selecting a screen changer.
Material Properties: The melting point, melt index, corrosivity, and flowability of raw materials also influence the choice of screen changer. For example, highly corrosive materials require screen changers with excellent corrosion resistance.
Production Costs: Different types of screen changers vary significantly in price. Comprehensive consideration of budget and production efficiency is essential.
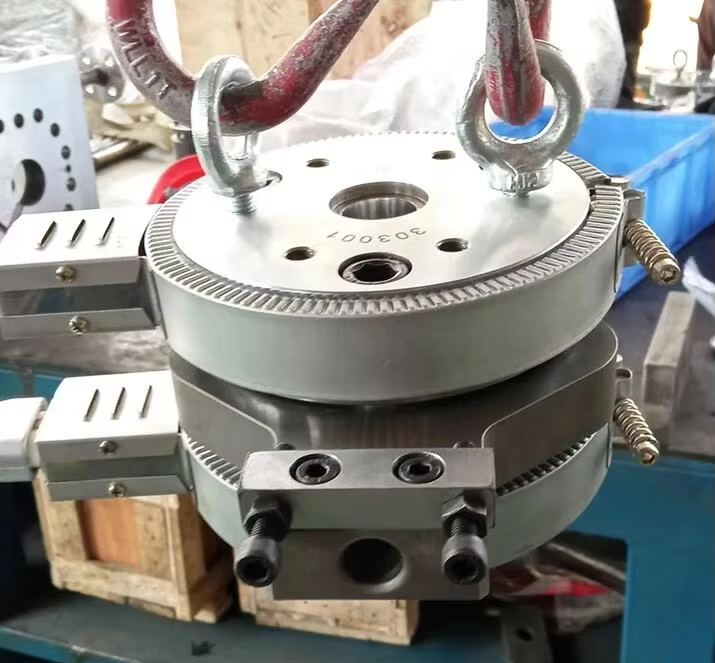
In summary, selecting a screen changer for plastic sheet extrusion necessitates a holistic assessment of production demand, process requirements, user demands, material properties, and production costs. Depending on the specific circumstances, the appropriate type of screen changer can be chosen to enhance production efficiency and product quality.
Email: info@battemachinery.com
WhatsApp: +86 158 38331071