What is the application of the screen changer for air-cooled plastic granulators?
The application of the screen changer for air-cooled plastic granulators is primarily manifested in the following aspects:
I. Application Fields
The screen changer for plastic granulators is primarily utilized in production areas that require uninterrupted material flow and high continuity during screen changes, such as:
Plastic Granulation: Involves heating, melting, and extruding plastic raw materials into granules of specific shapes to meet subsequent production process requirements.
Pipe Production: For the production of pipes like PE, PP, PPR, and PERT, the screen changer ensures both the continuity of production and the quality of the pipes.
Production of Sheets and Plates: During the manufacturing of sheets and plates, the screen changer plays a crucial role in maintaining production continuity and product stability.
Cast Film, Non-woven Fabrics, Chemical Fiber Spinning, etc.: These fields also demand high production continuity, and the screen changer finds extensive application in these areas as well.
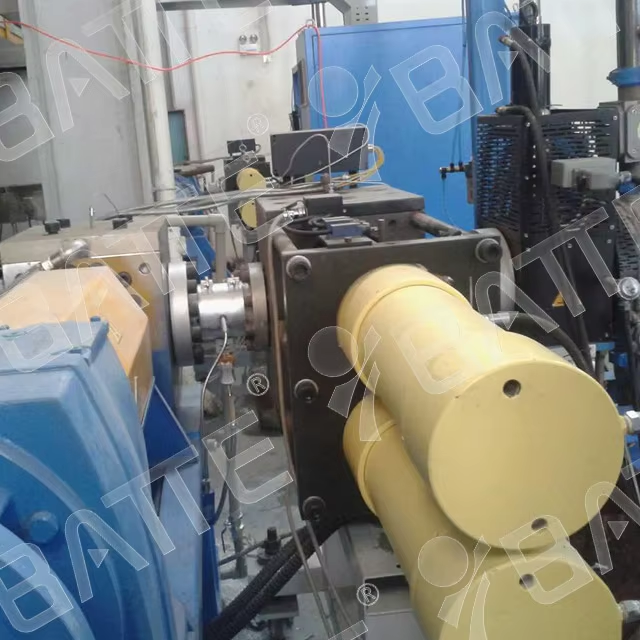
II. Working Principle and Performance Characteristics
Working Principle: The screen changer for plastic granulators is typically a double-column, double-station type. During operation, two screens work simultaneously. When a screen change is necessary, the hydraulic station is activated to perform the screen change action, enabling alternating operation between one screen working and the other being replaced. Through the material guiding and venting devices, air within the flow channel is thoroughly expelled, achieving uninterrupted screen changes without material leakage, maintaining material flow continuity, minimizing material pressure fluctuations, minimizing impact on production, and ensuring good continuity.
Performance Characteristics:
Dual Screens Working Simultaneously: Enhances production efficiency and reduces downtime.
Uninterrupted Screen Changes: Ensures production continuity, avoiding production losses caused by downtime for screen changes.
Uninterrupted Material Flow: Guarantees stable product quality, avoiding quality fluctuations due to interrupted material flow.
Minimal Material Pressure Fluctuations: Reduces the impact of screen change operations on the production system, conducive to stable production operations.
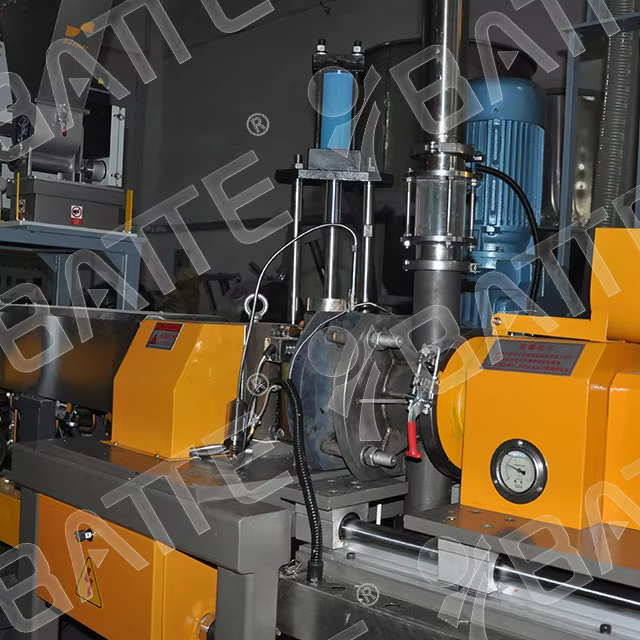
III. Precautions for Use
Pre-operation Checks: Before turning on the power, inspect the power cables and control system, confirm that the lubricating oil is sufficient, and check that the screen changer moves smoothly and the switches operate seamlessly.
Installation and Commissioning: When installing new screen plates, ensure that their dimensions and shapes comply with equipment requirements. Tighten the fixing screws with a torque wrench according to specified torque. During commissioning, first conduct a no-load run to check for any abnormal sounds or vibrations from the screen changer before gradually increasing the load to normal production conditions.
Cleaning and Maintenance: Maintain cleanliness and hygiene during screen changes to prevent impurities or dust from entering the equipment. Regularly clean residual materials inside the screen changer to ensure its normal operation and prolong its service life.
3333333333333
In summary, the screen changer for air-cooled plastic granulators has extensive applications in the plastic processing industry. Its unique working principle and performance characteristics bring numerous conveniences and advantages to production. Meanwhile, attention should be paid to operational norms, installation and commissioning, as well as cleaning and maintenance during use, to ensure the normal operation of the equipment and extend its service life.
Email: info@battemachinery.com
WhatsApp: +86 158 38331071