How to choose a screen changer for a raw fiber filament extruder?
There are various types of screen changers for filament extruder, each with its unique characteristics and applicable scenarios. Below are some common types of screen changers and their features:
1.Single-Plate Dual-Station Screen Changer
Features: It features two filter stations on a single slide plate, one in operation and one as a standby. When filter replacement is needed, the hydraulic system is activated to switch stations within a very short time (e.g., 1 second), pushing out the dirty filter station and bringing in the standby one, completing the screen change process.
Applicable Scenarios: Suitable for situations where continuous production is not critically essential, such as water ring pelletizing and hot cutting in recycled plastic production. However, note that an instantaneous interruption of material flow may occur during the station switch, causing material pressure fluctuations and reduced extrusion volume, which might manifest as partial strand breaks in underwater strand production, requiring re-traction of the strands.
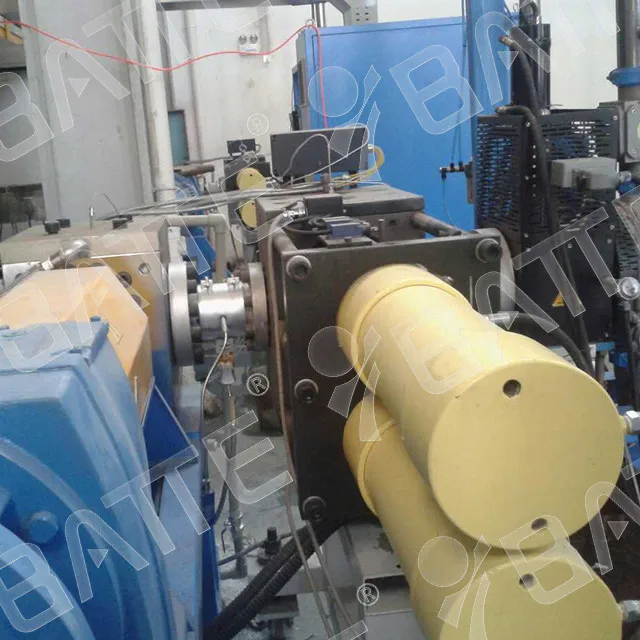
2.Double-Plate Dual-Station Screen Changer
Features: Similar to the single-plate design but with a double-plate configuration, potentially offering a larger filtration area and enhanced processing capabilities. The dual-station design also ensures continuous material flow during screen changes.
Applicable Scenarios: Ideal for applications requiring high production continuity and product quality, including direct extrusion (films, profiles, sheets, pipes, etc.), compounding (underwater pelletizing, water ring pelletizing, etc.), and raw material production and recycling.
3.Hydraulic Column Continuous Screen Changer
Features:
No Flow Interruption: Maintains constant material flow pressure and velocity during screen changes, eliminating instantaneous flow interruption and the need for re-traction. No downtime required for screen changes.
High Performance: Lacks mechanical seals, ensuring no material leakage under high pressure and temperature; monolithic structure withstands high pressure; premium alloy steel material with nitrogen treatment for extended service life; long-lasting integral engineering cylinders.
Precise Control: Paired with stroke position sensors for more accurate and controllable screen changes.
Safe and Energy-Efficient: Incorporates safety shielding for operator protection; utilizes internal heating devices for safety and energy efficiency.
Applicable Scenarios: Ideal for materials with good fluidity and high requirements for continuous production, allowing uninterrupted production during screen changes, such as cast film, fiber drawing, chemical fiber spinning, and other high-precision product manufacturing.
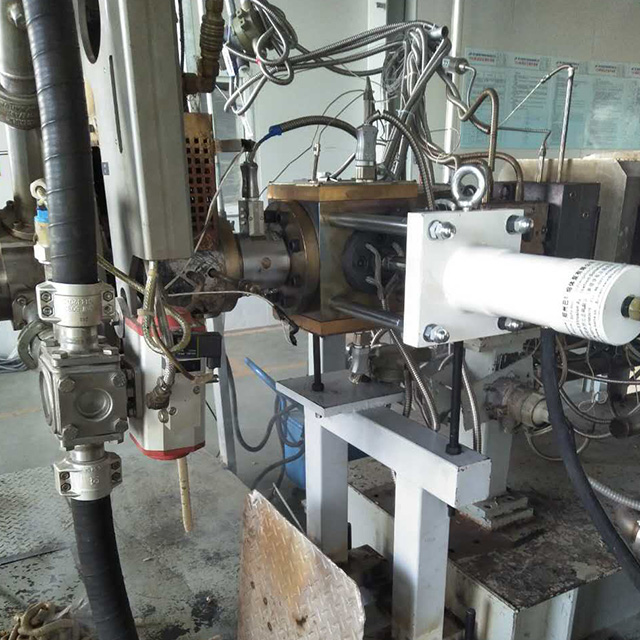
4.Mesh Belt Fully Automatic Screen Changer
Features: A fully automated screen changer using a mesh belt filter. It automatically advances the filter mesh based on material pressure, eliminating the need for manual intervention until the entire belt is consumed. The screen change process is smooth and stable, with minimal material pressure fluctuations (within a controllable range).
Applicable Scenarios: Suitable for various pelletizing processes and products with less stringent filtration precision requirements but high demands for production continuity, such as PP strapping bands, pipes, sheets, and plates.
5.Non-Continuous Screen Changer
Features: Requires manual operation for screen changes, with slower speeds, suitable for small-scale test lines or intermittent production processes. Its simple structure is accompanied by relatively significant pressure fluctuations during screen changes, potentially necessitating brief downtime.
Applicable Scenarios: Primarily used in the processing of solid-color materials, small-batch color masterbatch production, and compounding operations.
In summary, the diverse types of screen changers for filament extruders each have their unique characteristics. When selecting a screen changer, comprehensive consideration should be given to actual production needs, material properties, production processes, and other factors.
Email: info@battemachinery.com
WhatsApp: +86 158 38331071