Do the screen changers on the production line need regular maintenance?
The screen changer on the production line indeed requires regular maintenance to ensure its normal operation, extend its service life, and improve production efficiency and product quality. Here are some important considerations for the regular maintenance of the screen changer on the production line:
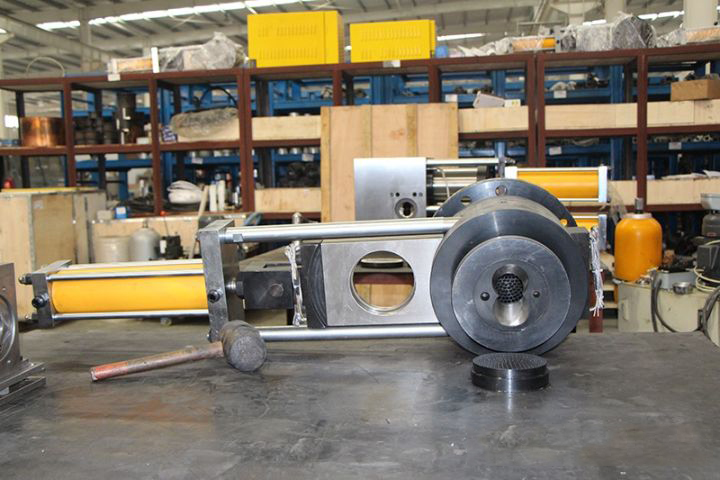
I. Necessity of Maintenance
Maintaining Equipment Performance: Regular maintenance ensures that all components of the screen changer are in good condition, preventing issues such as wear, clogging, or malfunctions from disrupting the normal operation of the production line.
Extending Equipment Lifespan: By regularly inspecting and replacing vulnerable parts like screens and mesh plates, the risk of premature equipment failure due to excessive wear is reduced, thereby extending the service life of the screen changer.
Improving Production Efficiency: A well-maintained screen changer can more efficiently filter impurities and particles from the molten material, ensuring product quality stability and reducing downtime caused by equipment failures, thereby enhancing production efficiency.
II. Contents of Regular Maintenance
Component Inspection: Regularly inspect all components of the screen changer, including mesh plates, screens, heaters, temperature sensors, motors, etc., to ensure they are functioning properly and free from wear or clogging. Additionally, check the oil circuit for blockages, ensure the oil level is appropriate, and verify the oil quality is clean.
Cleaning and Lubrication: Regularly clean the mesh plates, heaters, and screens to prevent the accumulation of debris and dirt. Meanwhile, lubricate moving parts such as bearings and guides with suitable lubricant to ensure smooth operation.
Replacing Vulnerable Parts: Based on wear and usage, regularly replace vulnerable parts like screens and mesh plates. Promptly replace damaged or severely clogged screens or mesh plates to maintain the normal operation of the screen changer.
III. Maintenance Precautions
Operational Norms: During maintenance, strictly adhere to operational norms to prevent component damage or equipment failure due to improper handling. For instance, when replacing mesh plates, follow prescribed steps to avoid excessive force that could deform or damage them.
Safety Precautions: When disassembling or inspecting the equipment, turn off the power to prevent electrical accidents. Also, during cleaning and lubrication, be mindful of preventing debris and lubricant from entering eyes or skin, which could cause harm.
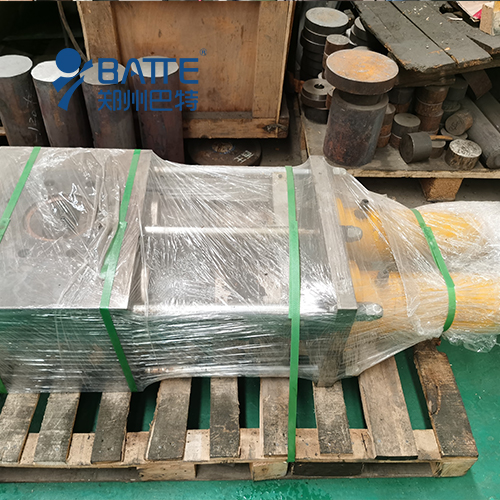
Maintaining Records: Establish and maintain records of the screen changer's maintenance, including details of inspections, cleaning, lubrication, and the replacement of vulnerable parts, along with the dates and personnel involved. By doing so, you can better track the maintenance status of the equipment, promptly identify and address issues, and ensure its smooth operation and extended lifespan.In conclusion, the screen changer on the production line necessitates regular maintenance. Through regular maintenance, we can ensure the normal operation of the screen changer, extend its service life, and improve production efficiency and product quality.
Email: info@battemachinery.com
WhatsApp: +86 158 38331071