What are the characteristics of the application of screen changers in plastic extrusion production lines?
The application of screen changers in plastic extrusion production lines exhibits several notable characteristics, which are primarily manifested in the following aspects:
I. Filtering Effect and Quality Assurance
Filtering Impurities: The screen changer effectively filters out foreign particles and impurities from the plasticized material flow through its internal screens. This includes aged or degraded particles, low-precision particulates in recycled materials, various non-plastic substances in recyclates, and incompatible plastics. This function is crucial for enhancing product quality.
Adjustable Quality: The screen changer allows for the installation of screens with different precision levels (i.e., mesh sizes) based on process requirements, meeting the diverse demands of product process grades and thereby ensuring stable product quality.

II. Improved Production Efficiency and Benefits
Continuous Screen Change: The widely adopted continuous screen change technology in modern plastic extrusion lines enables rapid screen replacement without stopping the machine. This not only guarantees the stability of product quality but also significantly enhances production continuity, minimizing production losses due to downtime for screen changes.
Cost Reduction: By eliminating downtime for screen changes, waste materials and energy consumption are reduced, thereby lowering production costs. Additionally, high-quality screens and screen changers decrease the defect rate caused by impurity contamination, further boosting economic efficiency.
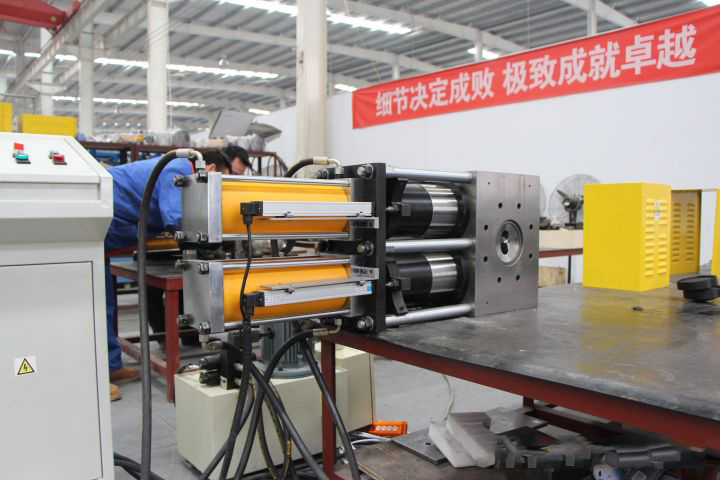
III. Structural Design and Operational Convenience
Flow Channel Design: The screen changer typically features a short flow channel design, minimizing temperature and pressure variations after the material flows through it. This design contributes to maintaining the stable state of the plastic melt and enhancing product uniformity.
High Load Capacity: The screen changer is capable of withstanding high material flow pressures, offering a distinct advantage in situations involving high-pressure extrusion of materials like polymers.
Ease of Operation: The screen changer boasts a relatively simple structural design and convenient connections, facilitating seamless integration with various sizes of single-screw and twin-screw extruders. Moreover, its operation is straightforward, enabling operators to quickly become proficient after training.
IV. Adaptability and Customization
Strong Adaptability: The screen changer is suitable for various plastic extrusion production lines, including those for plastic sheets, plates, films, pipes, and pellets. It also caters to different material compositions and production processes.
Customized Services: Tailored services are available based on specific customer needs. For instance, anti-corrosion treatments or the use of corrosion-resistant materials can be provided for corrosive materials. Additionally, customized heating solutions using thermal media can be offered upon request.
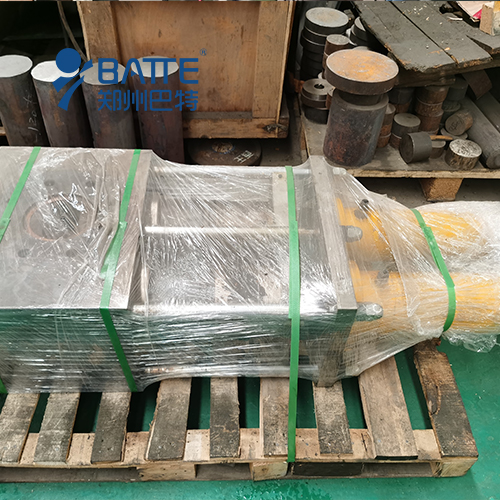
In conclusion, the application of screen changers in plastic extrusion production lines is characterized by impurity filtering, adjustable quality, improved production efficiency and benefits, rational structural design, operational convenience, and strong adaptability. These attributes make screen changers an indispensable and critical component in plastic extrusion production lines.
Email: info@battemachinery.com
WhatsApp: +86 158 38331071