Comprehensive Analysis of Hydraulic Screen Changers: Applications, Structure, Advantages, and Operation
Hydraulic screen changers are widely used in plastic extrusion, rubber processing, and ceramic manufacturing to filter impurities and ensure product quality. Featuring a dual-channel and dual-station design with a rigid sealing structure, they are suitable for high-temperature and high-pressure environments, enhancing productivity.
1.Plastic Extrusion
Hydraulic screen changers play a crucial role in the plastic extrusion process. They filter out impurities in the plastic melt, ensuring the quality and purity of plastic products. Specific application scenarios include:
Granulation processes for common plastics such as polyethylene (PE), polypropylene (PP), and polyvinyl chloride (PVC): Hydraulic screen changers effectively filter out impurities and unplasticized particles in the raw materials, improving the purity and quality of plastic granules.
Sheet extrusion, profile extrusion, and pipe production: Hydraulic screen changers provide clean plastic melts in these processes, ensuring the quality of the final products.
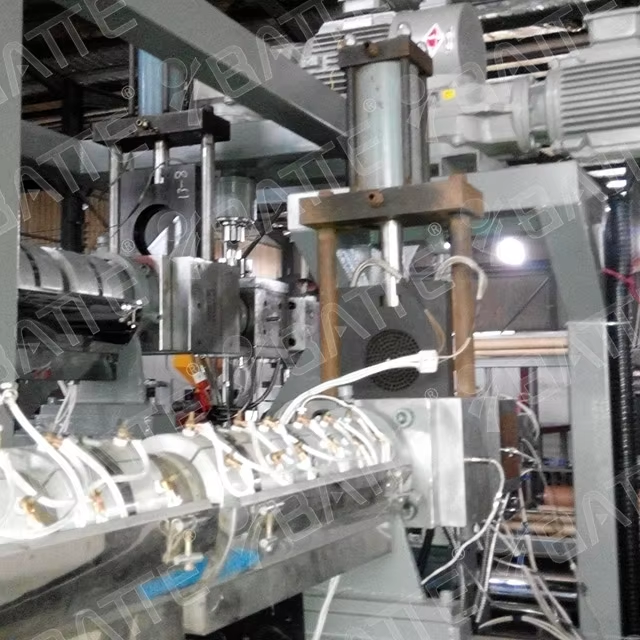
2.Rubber Processing
Hydraulic screen changers are also widely used in the rubber processing industry, particularly in rubber extrusion lines. They filter out impurities in the rubber melt, ensuring the quality and consistency of rubber products.
3.Ceramic Manufacturing
In ceramic extrusion lines, hydraulic screen changers play an important role as well. They filter out impurities in ceramic raw materials, ensuring the purity and quality of ceramic products.
II. Structural Characteristics and Technical Parameters of Hydraulic Screen Changers
Dual-Channel and Dual-Station Design: Dual-column, dual-station hydraulic screen changers utilize two stations working simultaneously. During screen changing, one screen is in operation while the other is being replaced, ensuring the continuity of the production process.
Rigid Sealing Structure: Ensures no leakage, guaranteeing the stability of the production process.
Optimized Material Introduction and Ventilation Structure: Reduces pressure fluctuations during screen changing, ensuring continuous and stable product production.
Maximum Operating Temperature of 350°C, Maximum Working Pressure of 50 MPa, Maximum Pressure Difference of 20 MPa, and Applicable Melt Viscosity Range of 100-20,000 Pa·s.
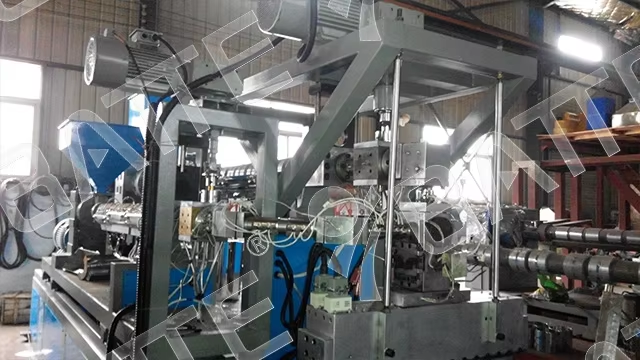
III. Advantages and Operation Methods of Hydraulic Screen Changers
Hydraulic screen changers utilize a hydraulic system for screen changing, featuring high automation, reduced downtime, and increased productivity. They are suitable for high-temperature, high-pressure, and corrosive conditions, providing a stable filtration rate and ensuring product uniformity and consistency.
Email: info@battemachinery.com
WhatsApp: +86 158 38331071