Dual-Plate Dual-Station Screen Changer: Structural Principle, Application Fields, and Prominent Features
I. Structure and Principle of Dual-Plate Dual-Station Screen Changer
The dual-plate dual-station screen changer primarily consists of two filter plates, the main body of the screen changer, a hydraulic system, a control system, and other components. Its working principle is as follows:
1. Working State:
During normal operation, the plastic melt enters the screen changer from the extruder and is diverted into two parallel flow channels. It is then filtered through the mesh screens on the two filter plates respectively to remove impurities.
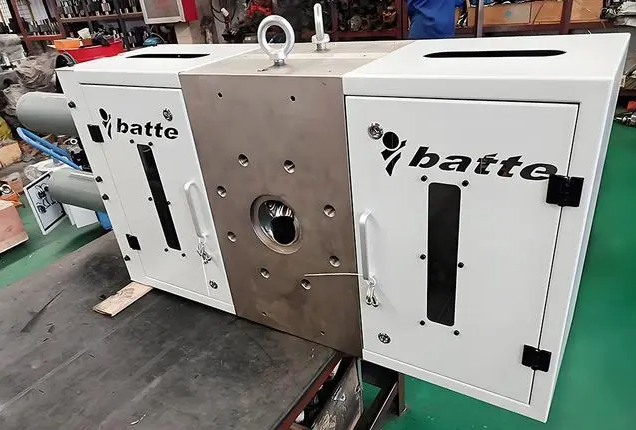
2. Screen Changing Process:
When the mesh screen on one filter plate needs to be replaced, the hydraulic system drives that filter plate out of the main body of the screen changer, while the mesh screen on the other filter plate continues to work, ensuring production continuity. The removed filter plate can undergo mesh screen replacement and cleaning operations, and after completion, it is pushed back into the main body of the screen changer by the hydraulic system to continue filtering.
II. Application of Dual-Plate Dual-Station Screen Changer
The dual-plate dual-station screen changer is suitable for almost all polymer melt filtration and can be used in conjunction with different standard single-screw/twin-screw extruders. The product is applicable to the production of chemical fibers, blown films, flat films, cast films, pipes, sheets, wires, fibers, granulation, recycling, packaging straps, and other products. The mesh screen specifications of the dual-plate dual-station screen changer are usually between 80mm and 250mm, with a maximum output of 4000KG/H.
III. Characteristics of Dual-Plate Dual-Station Screen Changer
High Filtration Efficiency: With two filter plates working simultaneously, the filtration area is double that of a single-plate screen changer, effectively filtering impurities in the material, improving filtration efficiency, and ensuring the quality of the extruded product.
Continuous Screen Changing: During screen changing, one screen works while the other is replaced, with rapid switching via the hydraulic system or other drive devices. The entire process does not require interrupting the material flow, achieving continuous screen changing, greatly improving production efficiency, and reducing issues such as wasted production time, unstable product quality, and material loss due to downtime for screen changing.
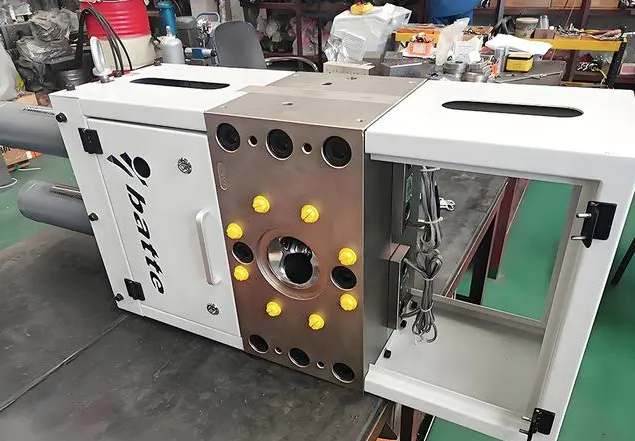
High Production Stability: Continuous filtration during screen changing does not cause significant fluctuations in extruder production, ensuring the stability of product quality, facilitating the production of uniform and consistent products, and reducing the rate of defective products.
Wide Application Range: It can withstand high melt pressure and meet the extrusion production requirements of all polymers, widely used in the production of chemical fibers, blown films, flat films, cast films, pipes, sheets, wires, fibers, granulation lines, recycling, and many other fields.
Excellent Sealing Performance: It adopts a reliable sealing structure, such as processing a circulating water channel on the side edge of the sliding plate seal surface and introducing cooling water to cool and solidify the material at the edge, thereby achieving sealing. This fundamentally eliminates leakage, ensures stable operation of the screen changer in high-pressure, high-temperature environments, prevents material leakage, and avoids pollution to the production environment and material waste.
Easy Operation and Maintenance: Screen changing is convenient and fast, generally completed through simple operations such as operating the handle buttons on the hydraulic station, with minimal screen changing waste. At the same time, its structure is relatively simple, making it easy for daily maintenance and reducing the labor intensity and maintenance costs for operators.
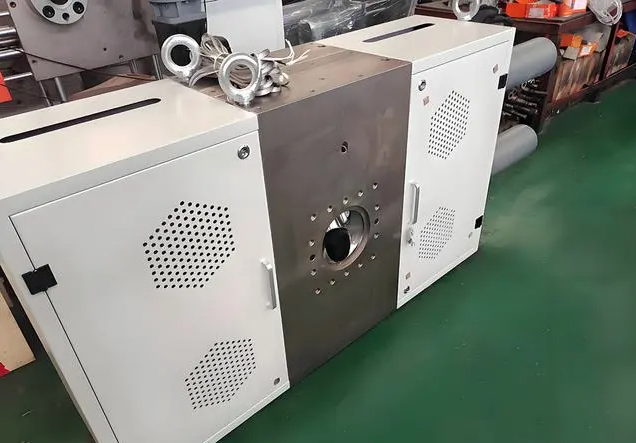
Heating and Insulation Design: Heating devices such as heating rods are usually installed on the sliding plate to heat and insulate the standby filtration station, making its temperature close to the production temperature, ensuring the stability of the material temperature after screen changing, and further ensuring the consistency of product quality.
Email: info@battemachinery.com
WhatsApp: +86 158 38331071