How to Choose a Screen Changer for PET, PA, and PVC Plastic Film Extrusion?
When selecting a screen changer for PET, PA, and PVC plastic film extrusion, multiple factors need to be considered to ensure it meets specific production requirements and process conditions. Here are some key selection points:
Material Characteristics
Melting Point and Melt Flow Index (MFI): PET, PA, PVC, and other plastic materials have different melting points and MFI, which affect the choice of screen changers. Materials with higher melting points require screen changers that can withstand higher temperatures, while materials with higher MFI may need larger filtration areas to prevent clogging.
Corrosiveness and Fluidity: Some plastic materials may be corrosive, necessitating the selection of screen changers made from corrosion-resistant materials. Additionally, the fluidity of the material will influence the design of the screen changer. Materials with poorer fluidity may require greater pressure and flow rates to ensure smooth extrusion.
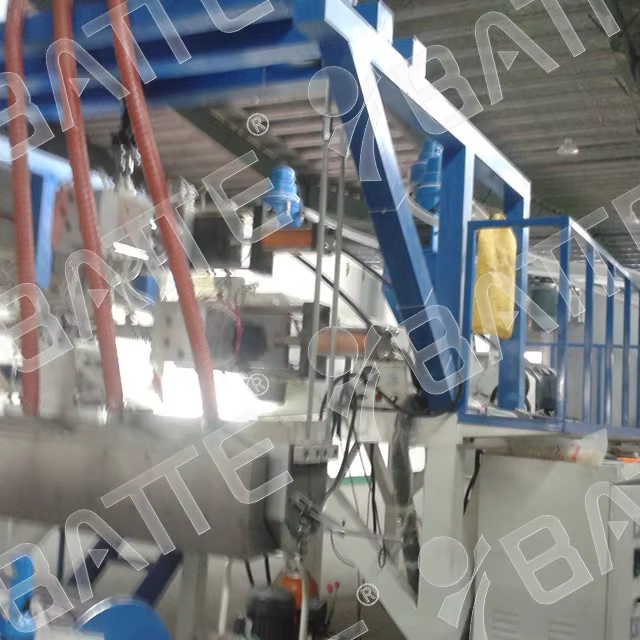
Production Needs
Product Continuity: Depending on the type of product being produced, the requirements for production continuity may vary. For example, strand granulation requires uninterrupted strands, while cast film production demands minimal pressure fluctuations during screen changes. Therefore, it is necessary to choose a screen changer that meets specific production needs.
Extruder Type: Single-screw and twin-screw extruders have different requirements for screen changers. Generally, the filter diameter should not be less than the screw diameter to ensure effective melt filtration.
Screen Changer Performance
Filtration Area: Select a screen changer with an appropriate filtration area based on the impurity ratio of the raw material and the recommendations of the equipment manufacturer. An excessively large filtration area may result in a bulky and costly screen changer, while an overly small area may lead to frequent clogging and affect production.
Screen Changing Method: Screen changers come in manual and automatic types. Manual screen changing requires downtime, affecting production efficiency, while automatic screen changing can be performed without stopping the machine, reducing production interruptions. Choose the appropriate screen changing method based on production needs.
Pressure Stability: The screen changer should be able to withstand the maximum pressure of the material flow to prevent leakage or difficulty in pushing and pulling. Therefore, when selecting, it is necessary to understand the maximum pressure value of the material flow and choose the appropriate screen changer model accordingly.
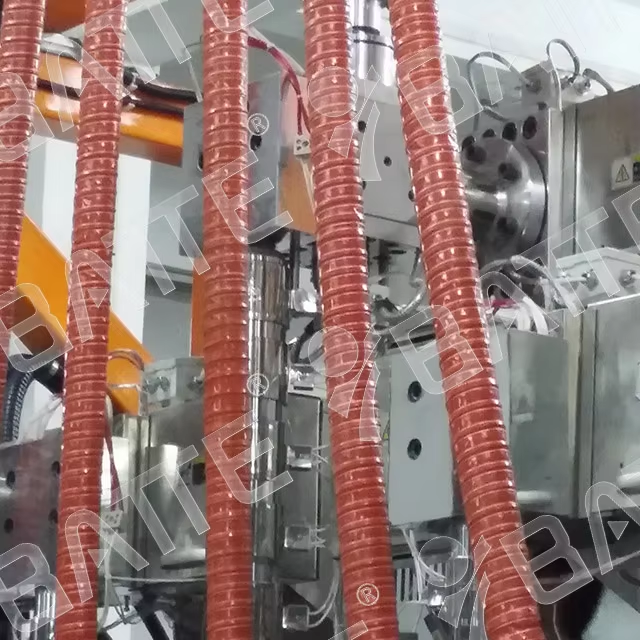
Other Factors
Cost and Maintenance: The cost of a screen changer includes both purchase and maintenance costs. When selecting, it is necessary to comprehensively consider cost-effectiveness and choose a product with high performance-to-price ratio. At the same time, consider the ease of maintenance and maintenance costs, opting for a screen changer that is easy to maintain and service.
Brand and Reputation: Choosing a well-known brand and a manufacturer with good reputation can ensure the quality of the product and the reliability of after-sales service. This helps reduce production risks and improve production efficiency.
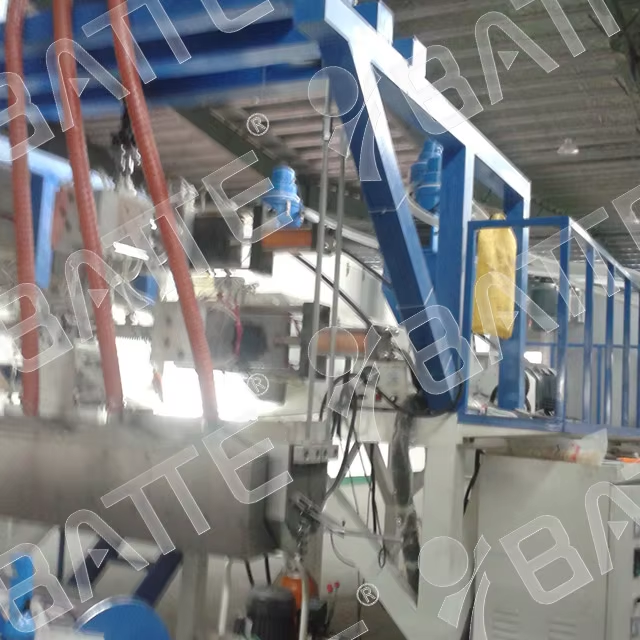
In summary, when selecting a screen changer for PET, PA, and PVC plastic film extrusion, it is necessary to comprehensively consider material characteristics, production needs, screen changer performance, and other factors. By carefully evaluating and comparing different options, the most suitable screen changer for specific production environments and process conditions can be found.
Email: info@battemachinery.com
WhatsApp: +86 158 38331071