Selection and configuration of screen changers for recycled plastic extruders
The selection and configuration of screen changers for recycled plastic extruders requires comprehensive consideration of multiple factors. Here are some specific selection points:
Production Output and Material Characteristics
Production Output: Based on the extruder's production capacity, choose a screen changer that matches it. Generally, the filtration capacity of the screen changer should be slightly higher than the extruder's output to ensure timely and effective filtration of impurities, preventing impurities from entering the product due to the filtration speed not matching the extrusion speed.
Material Characteristics: Recycled plastics have complex compositions and may contain different types of impurities, fibers, metal particles, etc. Select an appropriate screen changer based on specific material characteristics. For example, for recycled plastics containing more fibrous impurities, a mesh belt screen changer with better filtration effects can be chosen. For recycled plastics with higher viscosity, a screen changer with a larger filtration area and lower pressure loss should be selected to ensure smooth extrusion of the material.
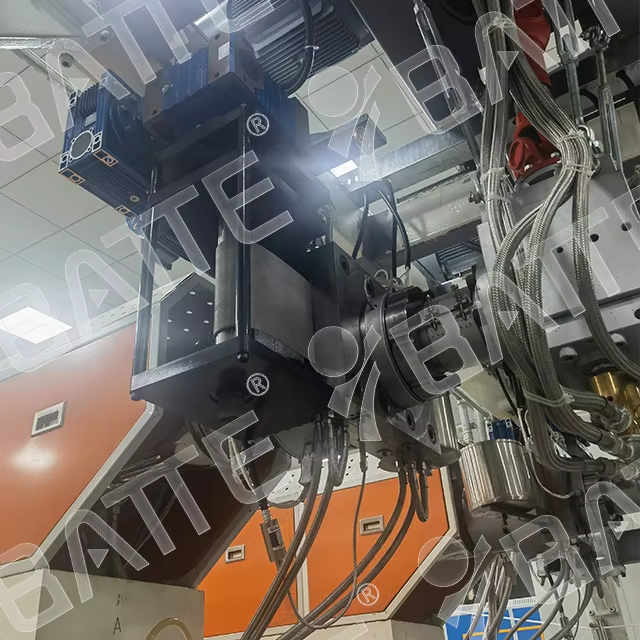
Extruder Type and Model
Single-screw Extruder: Typically, a single-plate double-station quick screen changer or a manual screen changer can be selected. If the production scale is small and the screen changing frequency is low, a manual screen changer can meet the demand. If there are certain requirements for production efficiency, a single-plate double-station quick screen changer can be chosen.
Twin-screw Extruder: Due to the higher output and better material plasticizing effect of twin-screw extruders, it is generally recommended to choose a double-column double-station screen changer or a mesh belt automatic screen changer to ensure filtration effect and production continuity. For example, when producing pipes, profiles, and other products on a large-scale twin-screw recycled plastic extrusion line, a double-column double-station screen changer is a better choice.
Process Requirements
Product Quality Requirements: If high requirements are placed on the quality of the extruded product, such as in the production of food packaging and medical plastics, a screen changer with high filtration accuracy and stability should be selected, such as a double-column double-station screen changer or a mesh belt automatic screen changer, equipped with high-precision filter screens.
Production Continuity Requirements: For situations requiring continuous production, such as large-scale recycled plastic pipe and film production, priority should be given to non-stop screen changers, such as double-column double-station screen changers and mesh belt automatic screen changers, to reduce production interruption time and improve production efficiency.
Screen Changing Methods
Manual Screen Changer: Low cost and simple operation, but requires shutdown during screen changing, suitable for small enterprises or situations with small production scales and low screen changing frequencies. For example, some small recycled plastic granulating factories with low output can choose a manual screen changer.
Hydraulic Screen Changer: Fast screen changing speed and capable of non-stop screen changing, but higher cost, suitable for situations with high requirements for production efficiency and continuity. Large-scale recycled plastic pipe and profile manufacturing enterprises usually choose hydraulic screen changers.
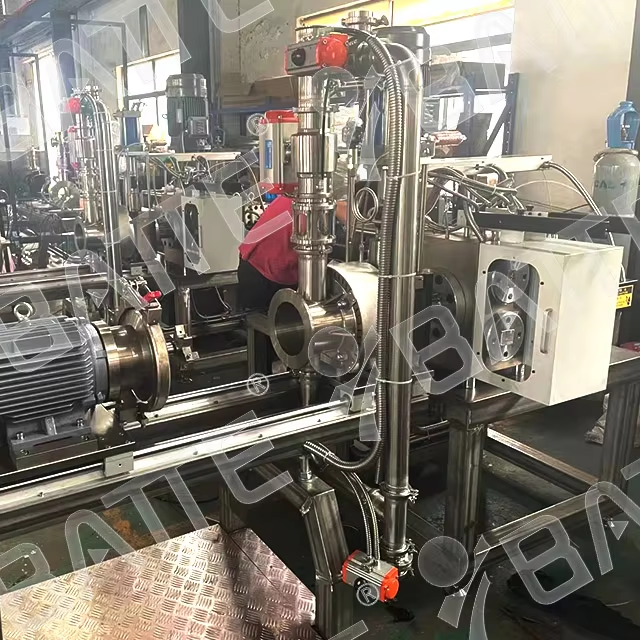
Price and Maintenance Cost
Price: The prices of different types, specifications, and brands of screen changers vary widely. Based on production needs, select a suitable screen changer according to the enterprise's economic strength. Generally, manual screen changers have the lowest price, mesh belt automatic screen changers have the highest price, and hydraulic screen changers fall between them.
Maintenance Cost: This includes filter screen replacement cost, equipment maintenance cost, and energy consumption. Choose a screen changer with a long filter screen lifespan, easy replacement, high equipment reliability, and low energy consumption to reduce long-term use costs. Some screen changers use special filter screen structures or materials to extend the lifespan of the filter screen, reducing the number of replacements and thus lowering maintenance costs.
Space and Installation Requirements
Space Limitations: Based on the installation space and layout of the extruder, choose a screen changer with the appropriate size and shape. Some screen changers are larger and require more installation space, while others have compact structures suitable for limited spaces.
Installation Method: There are various installation methods for screen changers, such as flange connections and threaded connections. Choose a screen changer that is easy to connect with the extruder and securely installed, ensuring that the installation process does not affect the normal operation of the extruder.
Email: info@battemachinery.com
WhatsApp: +86 158 38331071