Buying Guide for Plastic Pelletizing Screen Changers: Balancing Efficiency, Quality, and Compatibility
When selecting a plastic pelletizing screen changer, it is indeed necessary to consider multiple key points comprehensively to ensure it meets production demands, enhances production efficiency, and guarantees product quality. Below is a detailed analysis and supplement to the key points you have raised:
I. Clarify Production Needs
Production Materials: Different plastic materials may have varying requirements for the screen changer's material and screen type. For instance, some high-viscosity materials may necessitate sturdier screens and more robust screen-changing mechanisms.
Product Types and Output: Choose the appropriate screen changer size and type based on the product types being produced and the expected output. High-output production lines may require more efficient and automated screen-changing systems.
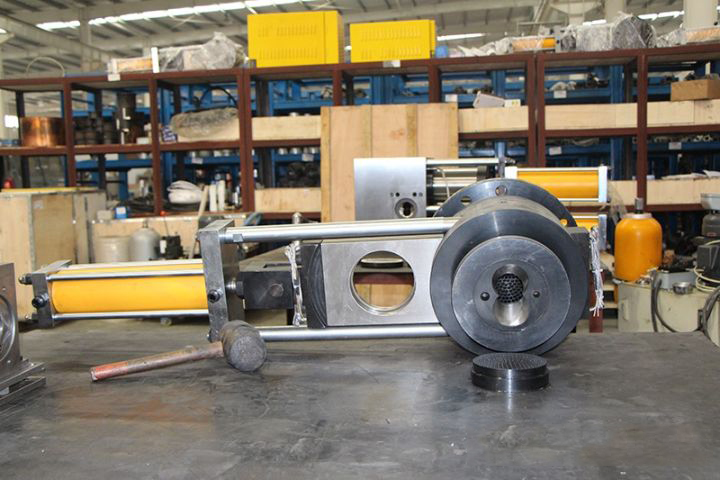
II. Understand Screen Changer Performance
Screen Types: Select the appropriate screen type based on production needs, such as metal mesh, sintered mesh, or ceramic mesh, each with its specific filtration precision and service life.
Filtration Precision: Ensure the screen changer's filtration precision meets product quality requirements to prevent impurities from entering the product.
Screen-Changing Time and Production Efficiency: Rapid screen-changing technology can reduce downtime and enhance production efficiency. Choosing a screen changer with rapid screen-changing capabilities is crucial for continuous production.
III. Consider Cost-Effectiveness
Price: Select a screen changer within budget to avoid overinvestment or underinvestment.
Quality: Opt for screen changers from well-known brands and reliable suppliers to ensure their quality and durability.
After-Sales Service: Excellent after-sales service support is vital for resolving issues during use, maintaining equipment performance, and extending service life.
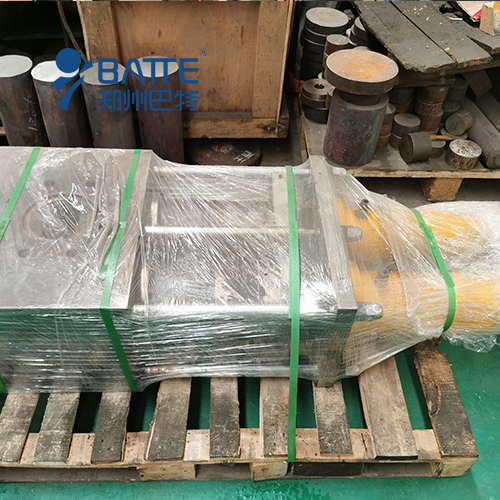
IV. Choose the Appropriate Configuration
Single-Plate, Dual-Station, or Dual-Column Large-Area Screen Changers: Select the suitable configuration based on specific production line needs. Dual-station screen changers allow for screen replacement without halting production, enhancing efficiency. Dual-column large-area screen changers are suitable for situations requiring the processing of large volumes of material.
V. Meet Special Needs
Recycled Plastic Pelletizing: Recycled plastics may contain impurities and irregular particles, necessitating the selection of screen changers with a pressure-stabilizing structure to ensure production continuity and stability.
Other Special Needs: Conditions such as high temperatures, high pressures, or corrosive environments also require the selection of corresponding special screen changers to meet production demands.
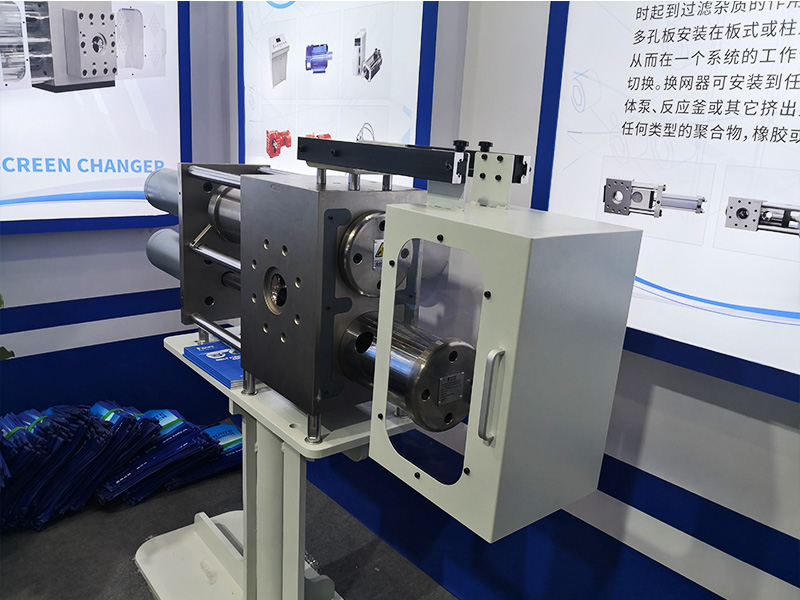
When purchasing plastic granulation screen changers, one should comprehensively consider production needs, performance requirements, cost-effectiveness, configuration schemes, and special needs. By carefully evaluating and comparing screen changers of different brands and models, select the one best suited to your production demands to ensure maximized production efficiency, product quality, and economic benefits.
Email: info@battemachinery.com
WhatsApp: +86 158 38331071