Screen Changer Selection Guide
In production processes, the selection of screen changers is critical. Here are eight key factors that must be comprehensively considered during selection:
Production Requirements
Based on annual production capacity, material composition, and process parameters, combined with the theoretical output of screen changers, ensure that actual production demands are fully met.
Process Requirements
Screen changers have diverse structures with varying impacts on the process. The most suitable model must be selected according to specific process requirements.
Equipment Characteristics
Manual screen changers are compact and energy-efficient but require manual operation. Models like single-plate dual-station and dual-column dual-station each have unique strengths and are suited for different scenarios.
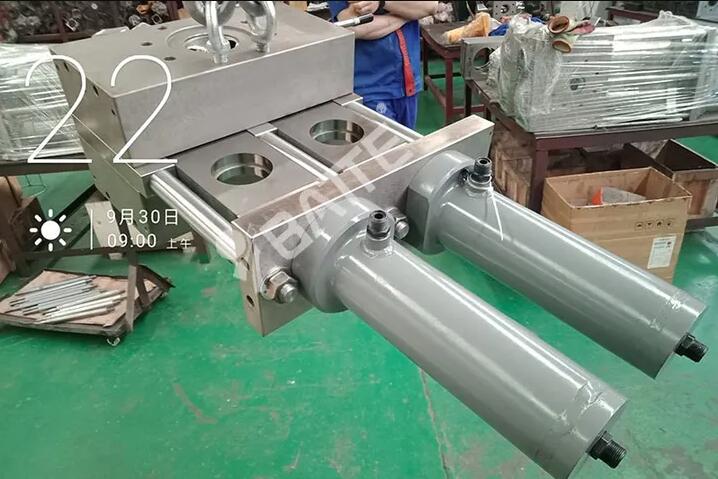
Drive Modes
Manual and non-manual screen changers each have advantages. Manual types are cost-effective and convenient, while non-manual types enable rapid screen changes but incur higher costs.
Screen Change Methods
Offline and online screen changes have distinct features. Continuous screen changers ensure production continuity and enhance efficiency.
Material Properties
Material viscosity and composition directly affect screen changer selection, requiring customized solutions.
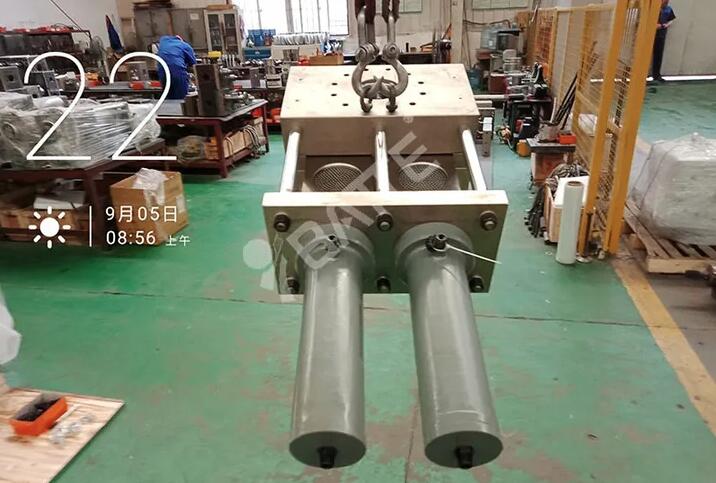
Economic Factors
Significant differences exist in price, structure, and drive modes. Comprehensive consideration of upfront costs and maintenance expenses is necessary to achieve optimal cost-effectiveness
User Requirements
User needs vary, such as stringent process requirements or reducing manual operations. During selection, user feedback must be fully incorporated.
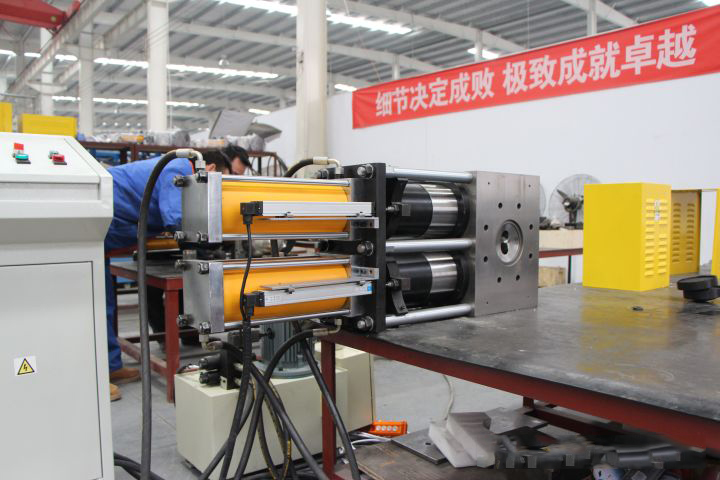
In conclusion, screen changer selection requires comprehensive evaluation of production demands, equipment features, material properties, economic factors, and user requirements to ensure precise selection and support efficient production operations.
Email: sale@meltpump.com
WhatsApp: +86 158 38331071