Comparative Analysis of Screen Changers by Structure, Drive Source, and Screen Changing Method
I. Classification by Structure
Plate-Type Screen Changers
Single-Plate Screen Changer: Features simple structure, compact size, easy installation, high cost-effectiveness, and wide applicability.
Dual-Plate Screen Changer: Equipped with two filter plates, enabling continuous operation during screen changes to enhance productivity. Minimal pressure fluctuation during screen change ensures stable product quality. Suitable for high-continuity production lines such as large-scale plastic manufacturing.
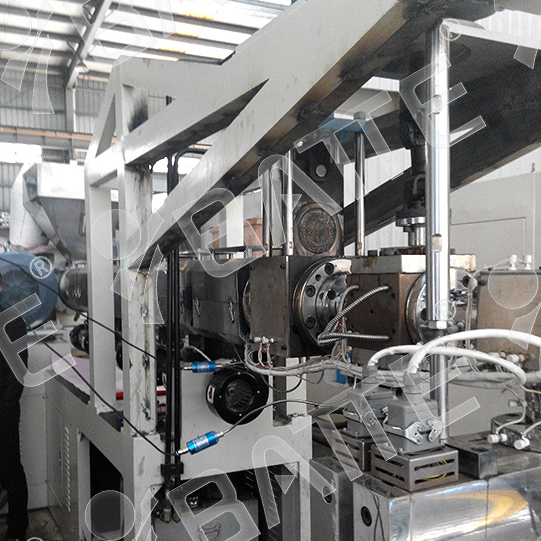
Cylindrical Screen Changers
Single-Cylinder Screen Changer: Compact design with small footprint, resistant to high temperatures and pressures, and long service life. However, its filtration area and throughput may be smaller compared to dual-cylinder models.
Dual-Cylinder Screen Changer: Features two cylindrical bodies for uninterrupted screen changes, ensuring stable material flow and minimal pressure fluctuations. Larger filtration area handles higher material volumes, ideal for medium to large-scale production lines like large plastic pipe extrusion.
II. Classification by Drive Source
Manual Screen Changers
Advantages: Compact size, easy installation, low cost, energy-efficient, and no external power source required. Simple operation and maintenance suit small enterprises or low-automation scenarios.
Disadvantages: Slow screen change speed requiring manual labor, high operator intensity, and production downtime during screen changes, impacting efficiency.
Hydraulic Screen Changers
Advantages: Rapid screen change with continuous operation capability, improving productivity and reducing waste. High automation simplifies operation via hydraulic system control, reducing labor intensity.
Disadvantages: Complex structure, higher costs, requires dedicated hydraulic stations, and demands strict hydraulic oil cleanliness and stability, leading to elevated maintenance costs.
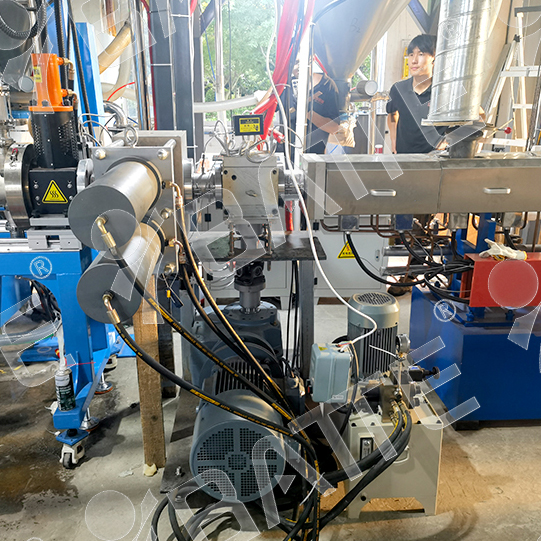
III. Classification by Operational Mode
Screen Changers Requiring Production Stoppage
Examples include single-plate single-station and single-cylinder single-station screen changers. Production must halt during screen changes, causing interruptions and efficiency losses. However, simpler structure and lower costs are advantages.
Non-Stop Screen Changers
Includes dual-station or quad-station screen changers. Standby filters engage during operation, enabling continuous production and higher efficiency. More complex structure and higher costs are trade-offs for uninterrupted operation.
Email: sale@meltpump.com
WhatsApp: +86 158 38331071