Hydraulic Screen Changer for Extruders: An In-depth Analysis of Standard and Customized Configurations
I. Overview of Standard Configurations
The standard configurations of hydraulic screen changers for extruders form the core of their basic functionalities, primarily encompassing several key components:
Screen Changer Body: This is the central structure of the hydraulic screen changer, responsible for installing the screen filter and executing screen changing operations. Its design must ensure stable operation under high-pressure and high-temperature conditions while facilitating rapid screen replacement.
Accumulator Hydraulic Pump Station: This component provides the necessary hydraulic power for the screen changer, ensuring swift, smooth, and reliable screen changing actions. The accumulator function helps maintain hydraulic system stability during screen changes and reduces energy consumption.
Heating Device: The heating device preheats the screen filter and plasticizing materials to ensure material fluidity during screen changes, preventing blockages caused by temperature drops. This contributes to improved production efficiency and product quality.
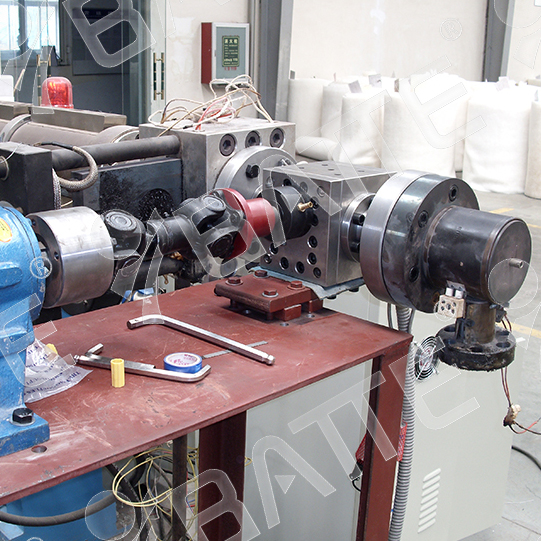
II. Detailed Explanation of Customized Configurations
Building upon standard configurations, hydraulic screen changers for extruders can be customized based on specific production needs and process characteristics to accommodate a broader range of applications:
Electrical Control Cabinet: Customized configurations may include an electrical control cabinet for automated control of the screen changer. Through programming and settings, the electrical control cabinet can precisely manage parameters such as screen changer startup, shutdown, and screen change timing, enhancing production process automation and efficiency.
Special Material Screen Filters: Customized screen filters made from special materials can be provided based on customer requirements for filtration accuracy and corrosion resistance. For instance, for highly corrosive materials, screen filters with superior corrosion resistance can be selected to ensure production process stability and safety.
Additional Safety Devices: To further enhance production safety, additional safety devices such as safety locks and pressure sensors can be incorporated into customized configurations. These devices provide extra safety measures during screen changes, preventing accidents caused by misoperation or equipment malfunctions.
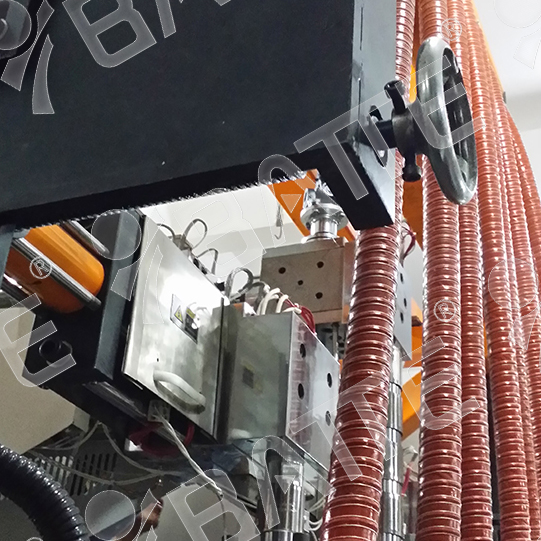
III. Application Areas and Advantages
Hydraulic screen changers for extruders are widely used in fields such as pelletizing, PE/PP/PPR pipe production, board manufacturing, sheet processing, pigment film production, non-woven fabric manufacturing, and chemical fiber spinning. In these areas, hydraulic screen changers offer robust support for production process continuity and product quality through their efficient, stable, and reliable screen changing performance.
Improved Production Efficiency: Swift and smooth screen changing operations reduce production downtime and enhance production efficiency.
Guaranteed Product Quality: Precise screen replacement and a stable hydraulic system ensure uniformity and consistency in material extrusion, thereby improving product quality.
Reduced Maintenance Costs: Standardized components and easily replaceable screen designs lower equipment maintenance costs and downtime.
Strong Adaptability: Customized configurations can be tailored to meet specific customer needs, accommodating various production processes and material characteristics.
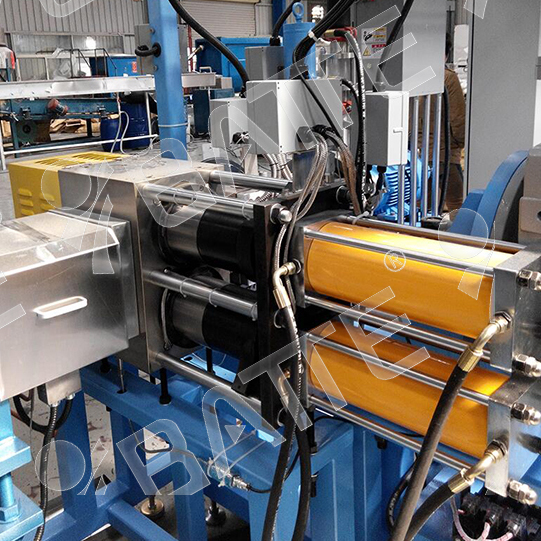
In conclusion, hydraulic screen changers for extruders play a crucial role in the extrusion production processes of materials such as plastics and rubbers due to their outstanding performance and wide application range. Whether in standard or customized configurations, they provide efficient, stable, and reliable screen changing solutions for customers.
Email: sale@meltpump.com
WhatsApp: +86 158 38331071