Screen changer use and function
Screen changer is the key filtration equipment in polymer material extrusion line, the main role is as follows:
First, continuous filtration of melt impurities
Intercept the solid impurities such as carbide, gel, unmelted particles in the molten polymer (e.g. black dots in plastic, foreign matter in rubber) through multi-layer metal filtering mesh.
Typical filtration accuracy range: 40-300 mesh (optional according to material characteristics)
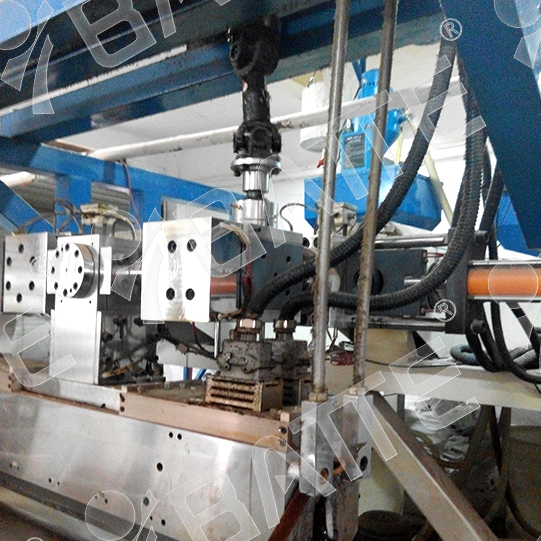
Guarantee product quality
Prevent impurities from entering the mold head and causing surface defects (such as holes in the film, uneven wall thickness of the pipe).
Especially important for optical grade products (e.g. PET sheet) and medical materials (e.g. catheters).
Protecting downstream equipment
Prevents clogging of die head runners and reduces the frequency of mold removal and cleaning.
Extend the service life of gear pumps and other precision parts
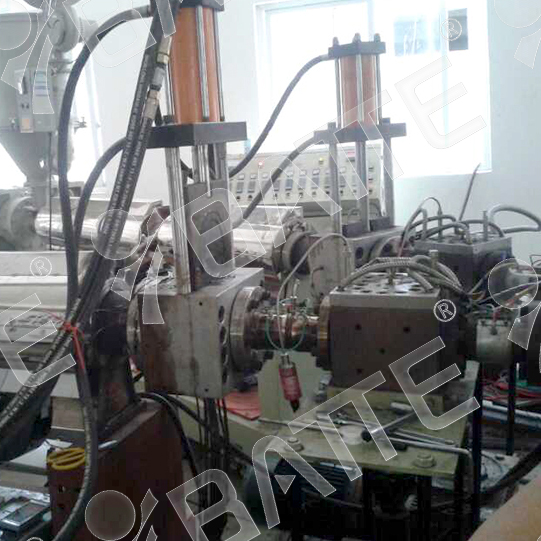
Realize non-stop production
Duplex design allows for quick screen switching during pressure buildup (switching time can be controlled to 1-3 seconds)
Typical working pressure range: 10-35MPa (depending on the viscosity of the material)
V. Adaptation to special process requirements
Handling of high impurity content melts in recycled material processing
Homogenizing melt flow when adding masterbatches
Email: sale@meltpump.com
WhatsApp: +86 158 38331071