Recycling filter for highly contaminated applications
The contaminated melt flows through the fixed, cylindrical strainer tube from the inside out. The micro-conical holes provide efficient filtration of contaminated melt. The contaminants are separated from the melt and then scraped by a rotating blade shaft from the surface of the strainer tube. The cooled discharge screw removes the collected contaminants from the machine out. The speed of the blade shaft/discharge screw can be adjusted depending on the throughput, contaminat level and discharge rate, thus ensuring a continuous working process with a clean, open filtration area with low melt loss.
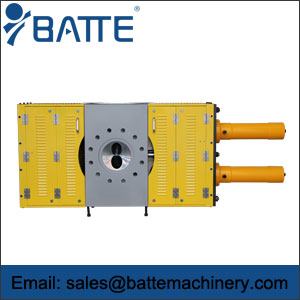
DeMatto’s firm uses multiple types of screen changers and melt filters. Slide screen changers use two screens and slide them from one side to the other. On the upside, these do not require any downtime. But the process is not without issues. “The problem with those is, if the screen pack is plugging off [contaminant catching on the screen], whatever that contaminant may be, you change screens, and there’s some dead space there. So there’s a risk of getting some contaminants through into your material.”